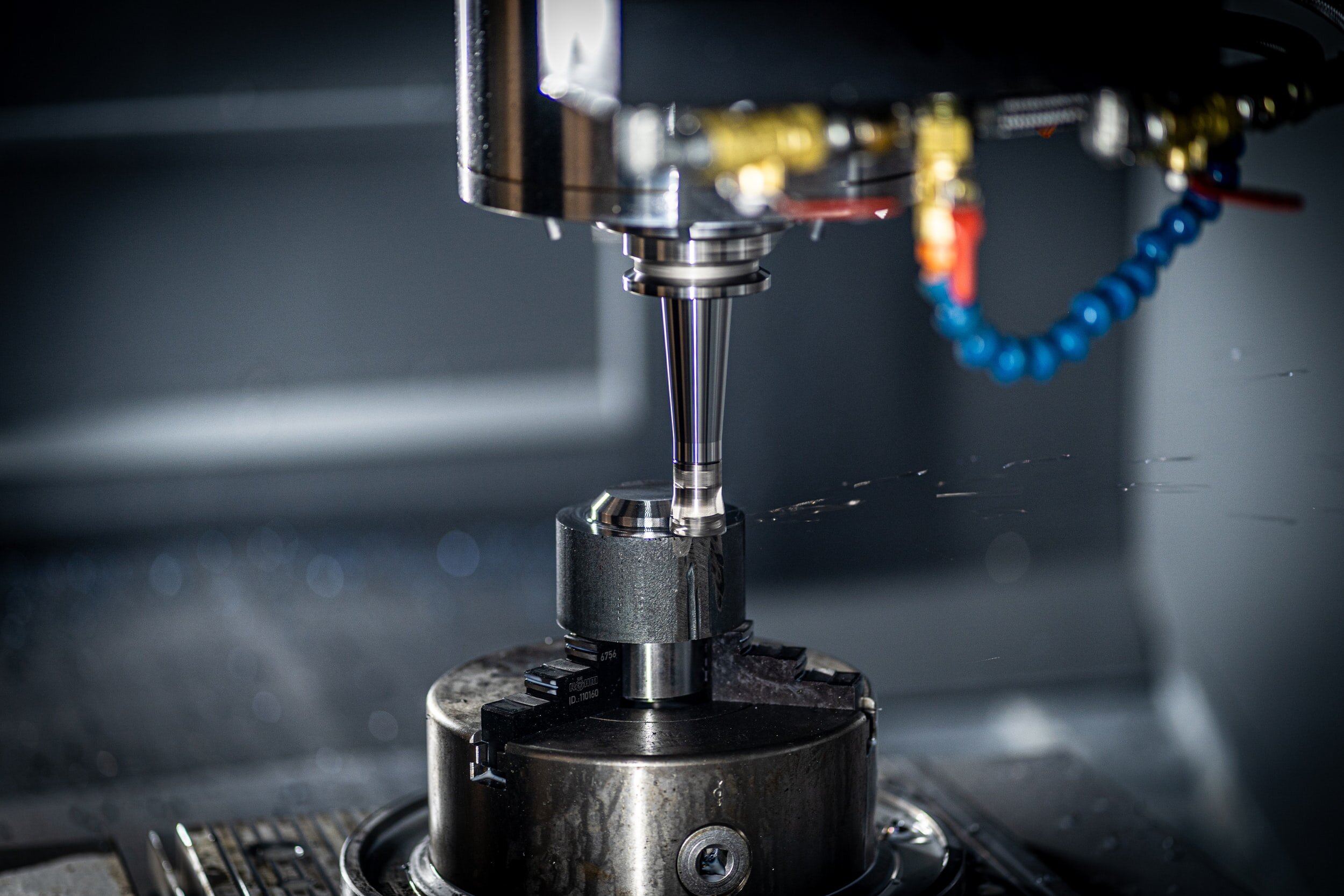
Manufacture and Test
Busek draws from thirty-five years of testing experience and world-class facilities.
Manufacturing
Decades of Making Thrusters
We’ve been making thrusters since 1985. With the experience of over thirty decades of Hall thruster development, our hardware is the best in the industry. We are experts at meeting rigorous spaceflight standards and qualifying for the most extreme environments. We provide products for the most demanding defense and commercial applications, and are proud to say that our products are manufactured and assembled exclusively in the USA.
The Highest Level of Quality and Mission Assurance
Busek is AS9100D and ISO 9001 certified. We incorporate Quality/Mission Assurance throughout the program cycle, from contract award, to product deployment. To maintain precision controls of our products, Busek utilizes ISO Class 8 certified Clean Rooms during the build and inspection phases of our products.
Our mission is to deliver high reliability products on time to military, aerospace, and related industries while meeting or exceeding customer expectations. We strive to continually improve quality and build strong relations with our customers, subcontractors, and suppliers to ensure product integrity and position Busek for future growth.
Available in batch sizes of one or thousands.
Between our four clean rooms and manufacturing partners, Busek has the capacity to manufacture thousands of thrusters. Intelligent choices in materials and parts reduces the cost and assembly complexity of each thruster. With thruster lead-times driven primarily by supply chains and test regiments, our technicians rapidly assemble thrusters once parts are in-house. Our extensive testing facilities can qualify every thruster that is delivered.
Design for Manufacturability
Each Busek thruster is designed with manufacturability in mind from the start. Instead of adding mass and cost adapting reference laboratory designs from outside licensors, Busek maintains the wide pool of expertise needed to make effective design decisions at every step of the process.
Our engineers use industry-standard geometric dimensioning and tolerancing via the ASME Y14.5 2009 Standard. All our materials are sourced and controlled by ASTM standards.
In-House Inspection
We maintain expertise in metrology and inspection for the range of our parts. With ultra-precise inspection equipment, we’ve able to accurately quantify our parts in every step of the process. After testing, we precisely scan our thrusters to determine and predict overall lifetime. With a cumulative total of decades of testing time, we can accurately retire risks that are impossible to quantify without performing long duration tests.
We maintain 3D X-Ray computed topography machines, optical comparators, high power microscopes, coordinate measurement machines, and an in-house machine shop to make sure our parts meet every specification.
Testing
Busek has a full complement of testing capabilities on site for all its variations of space propulsion systems. Our processes and methods are subject to continuous improvement to ensure the most reliable performance.
World class vacuum facilities.
We boast over twenty vacuum tanks and testing chambers. We have three massive vacuum tanks capable of testing our highest power thrusters, with state of the art pumping speed for minimal background pressure effects. Our torsional test stands are highly accurate, and our testing team has 50+ years of combined testing experience. We have decades of test data, from the smallest 100 W Hall thruster to our massive 20 kW thruster.
Cutting edge plasma diagnostics.
Over thirty years of experience testing and characterizing plasmas have taught us a lot. We design custom Langmuir probes, Faraday probes, RPA probes and test stands for the most accurate and reliable diagnostics. Our large collection of testing data gives us a strong baseline to compare experimental data with expected plasma characteristics.
Full Acceptance Testing.
Every thruster we manufacture is subject to rigorous acceptance testing to ensure the highest quality control. Our testing includes:
Dimensional & optical inspection
Magnetic field strength probes
Electrical functionality tests
Thermal-vacuum tests
Flow & leak tests
Shock/vibe
Performance measurements
Comprehensive plasma diagnostics